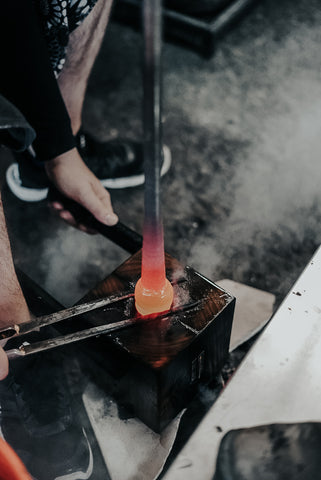
Every Dougherty Glassworks glass is made by hand in a multi-step process that involves glass, steel, wood and fire. The creation process blends centuries-old mold-making techniques with modern technology.
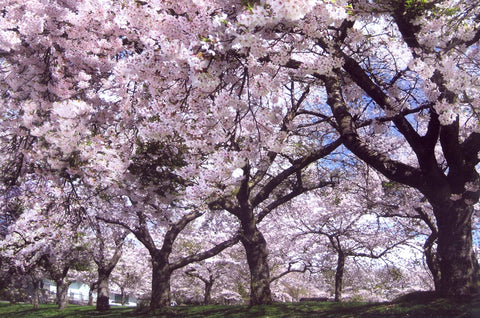
MOLD MATERIAL - CHERRY WOOD
First let’s look at the mold. Vancouver’s beautiful cherry trees are world-famous for their display of color every spring. These cherished trees are so sweet, in fact, that the wood is full of sugars. This makes cherry wood the finest choice for making the molds used for hand-blown glass. The wood for my molds was salvaged in Vancouver by my wife, who is an arborist.
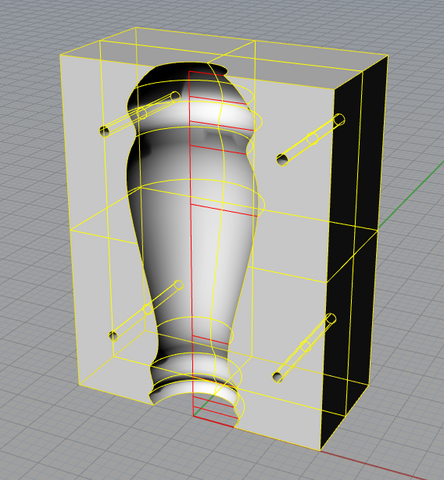
MOLD CREATION
I begin creating each glass using digital 3D modeling software. Once the design is finished, I send it to a CNC machine that cuts two identical halves of the mold into the wet cherry wood. I then add a hinge and handles to complete the mold, and store it underwater to maximize heat resistance and prevent cracking.
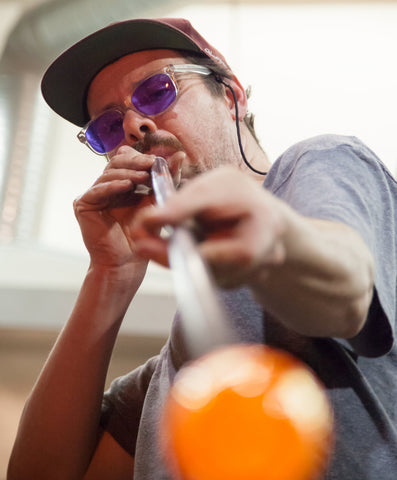
To make each glass, we first gather liquid glass from a large furnace onto the end of a stainless steel pipe. We then blow air through the pipe and into the white-hot glass, forming a bubble.
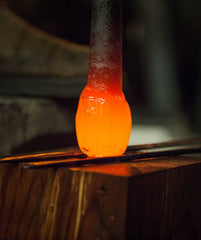
We re-heat the bubble in the glory hole until it is ready to be dripped into the wooden mold. We have our assistant close the mold and we blow into the pipe while spinning it to produce a seamless glass.
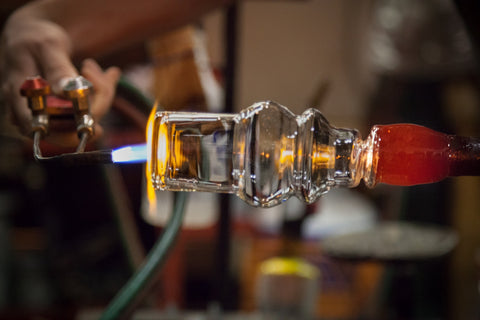
Once the glass has cooled enough to hold its shape, we remove it from the mold and we impress the Dougherty Glassworks stamp in the base, marking it as uniquely handmade.
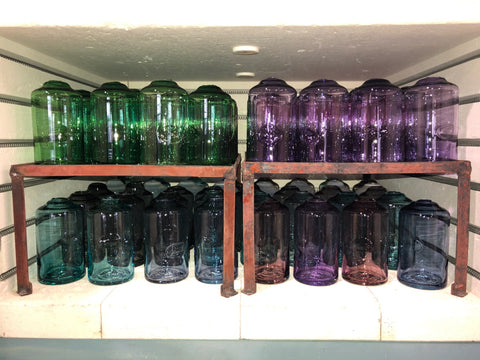
We then crack the glass off the pipe and put it in a pre-heated kiln for 12 hours of slow cooling (called annealing), after which it’s ready for final shaping and polishing.
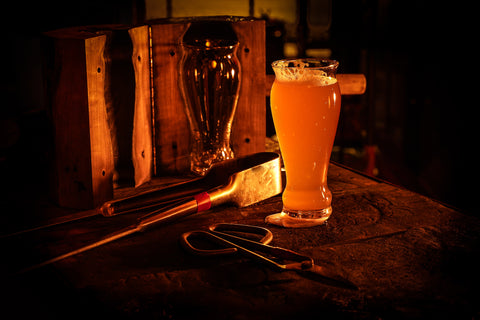